- Electrical conduit protects wires within a structure and is an integral part of large construction projects including data centers, utilities, underground transit systems, and bridges.
- Electrical conduit can be non-metallic and metallic, with various types within each category.
- Key considerations for choosing an electrical conduit type include weight, corrosion resistance, cable fault resistance, fire resistance, cost, and availability.
What is Electrical Conduit?
Electrical conduit is a raceway used to house and protect electrical wires within a building or structure. From data centers to underground subways to ports and bridges, electrical conduit is an integral part of the modern world around us.
There are several different conduit types available. The specified conduit for a project may be rigid or flexible and will offer varying degrees of protection from impact, corrosion, gases and vapors, moisture, fire, and even electromagnetic interference, depending on the needs of the installation environment. Environments that are wet, highly corrosive, or hazardous often require specialty conduit.
Electrical conduit may also be permitted per the National Electrical Code (NEC) for use in direct encasement (or direct burial) in concrete, which is common in commercial and industrial applications. Also, the ability to field bend conduit, as well as its allowable support spacings will impact how many fittings (couplings, elbows, connectors) are needed for a project and also have a direct impact on cost.
Metal Electrical Conduits
Rigid Metal Conduit (RMC):
RMC is typically composed of heavyweight galvanized steel and installed with threaded fittings. Known for being very strong, RMC is unfortunately one of the more expensive electrical conduits when it comes to both materials and labor. Aluminum is another material used for RMC, and may have additional coating applied to better resist corrosion.
Relevant NEC Codes: Article 344

Galvanized Rigid Steel (GRC):
Approved for indoor and outdoor applications, GRC is made from steel and is traditionally found in industrial and commercial applications, GRC has been a longtime industry standard and benefits from impressive impact resistance, as well as UV stability and the ability to protect from EMI (electromagnetic interference). Unfortunately, its heavy weight and poor field handling make GRC particularly expensive to install and susceptible to corrosion. GRC’s conductivity makes it prone to fault conditions in which the conduit and wire may weld together.
Relevant NEC Codes: Article 344
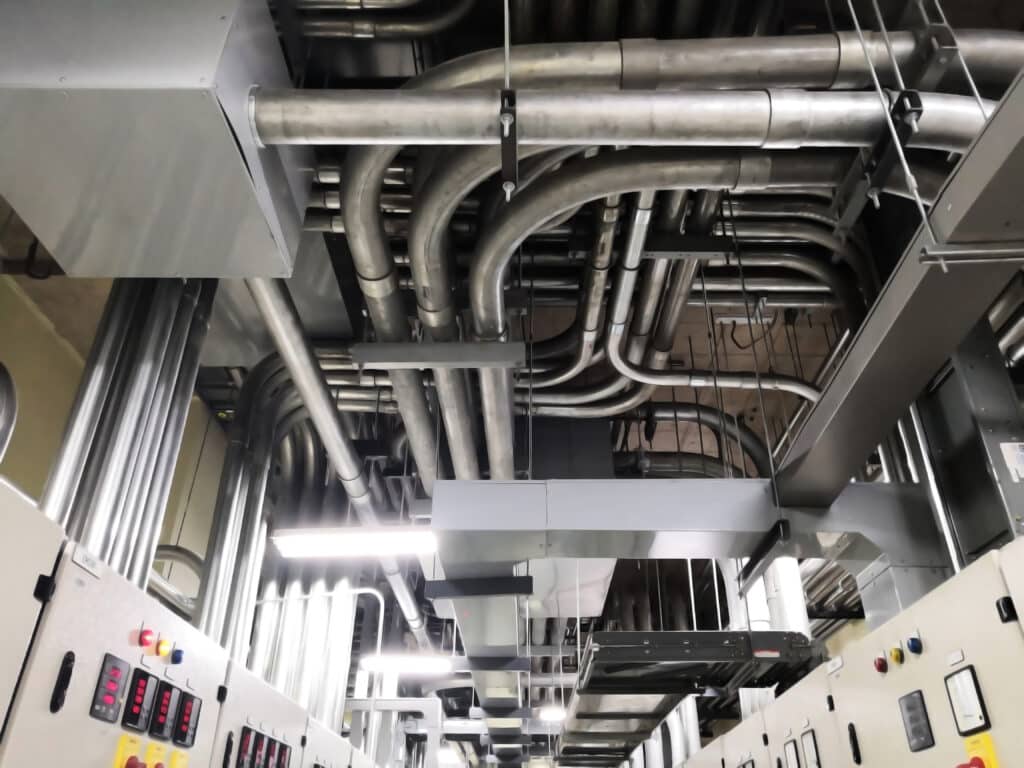
Intermediate Metal Conduit (IMC):
Approved for the same applications as RMC, IMC is a steel conduit that is slightly lighter than RMC and rated for outdoor use. It can be more cost-effective than RMC, available threaded or unthreaded, and may or may not be coated. Compared to GRC and RMC, IMC has much thinner walls that can handle more wire fill but is more susceptible to kink. IMC only goes up to 4 inches in trade sizes, so it is significantly smaller than other conduits.
Relevant NEC Codes: Article 342

Electrical Metallic Tubing (EMT):
Thin-walled and unthreaded, EMT is typically made of coated steel and used in place of GRC in commercial and industrial applications, though it is commonly found in residential applications as well. It can also be made of aluminum and is approved for use in concrete but is not permitted to be installed where subject to physical damage. EMT is not able to offer the same level of protection as GRC. It is easily bent but can not be field threaded because of its thinness. Common trade sizes run from .5 inch to 1.5 inches.
Relevant NEC Codes: Article 358

Non-Metal Electrical Conduits
Rigid Nonmetallic Conduit (RNC):
Non-metallic, unthreaded, smooth-walled tubing is available in multiple substrates including high-density polyethylene, PVC, and RTRC (fiberglass). The capabilities and specs vary by substrate but several forms of RNC are approved for underground or direct burial use.
Relevant NEC Codes: Article 352

RTRC Conduit:
Available in various wall thicknesses, RTRC (reinforced thermosetting resin conduit), or fiberglass conduit is created by tension-winding strands of fiberglass over a rotating mandrel, before impregnating the strands with resin and curing under high temperature, resulting in high flexural strength and high-temperature resistance. RTRC features the broadest range of corrosion resistance of all in-market conduit materials, as well as low burn-through, UV stability, superior temperature range (including excellent handling in low temperatures), and the ability to retain its original shape after impact. Its support distances are comparable with GRC, PVC-coated steel, and aluminum electrical conduit.
RTRC is significantly lighter in weight than traditional conduit materials, resulting in the lowest labor installation rates for most diameters per the National Electrical Contractors Association (NECA) Manual of Labor Units. In terms of raw material costs, it is one of the more affordable electrical conduit options. Phenolic RTRC meets NFPA 130 requirements and is suitable for speciality applications requiring low smoke, no flame, zero halogen, 2-hour fire-rated conduit for use in Class I Div 2 areas.
Relevant NEC Codes: Article 355
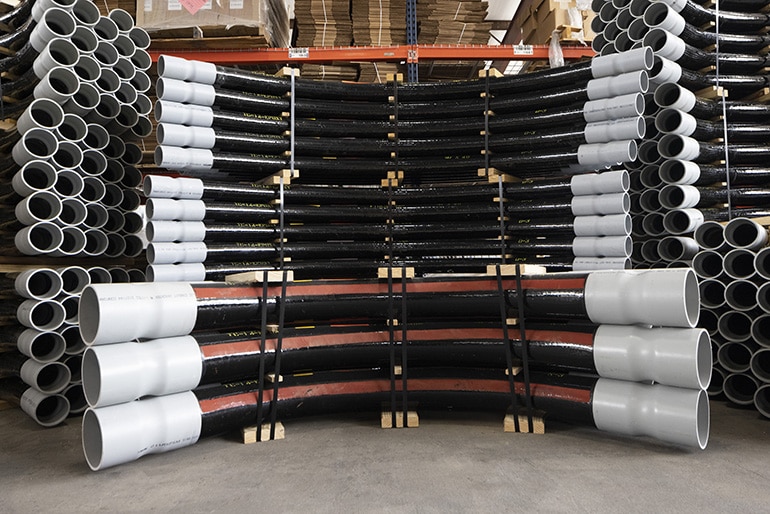
PVC Conduit:
Available in varying wall thicknesses and threaded, PVC is light and commonly used for applications requiring non-metal electrical conduit. PVC conduit is not recommended for use in direct sunlight due to poor UV stability. It is relatively easy to heat and field bend with the use of a hotbox conduit bender, but must be mounted to allow for expansion and contraction due to a high coefficient of thermal expansion, and may deform after installation in environments that are too hot. Traditionally PVC has been an inexpensive conduit, however, in recent years it has become more expensive and harder to source, due to ongoing supply chain issues. In these cases, American-made RTRC is often substituted.
Relevant NEC Codes: Article 352
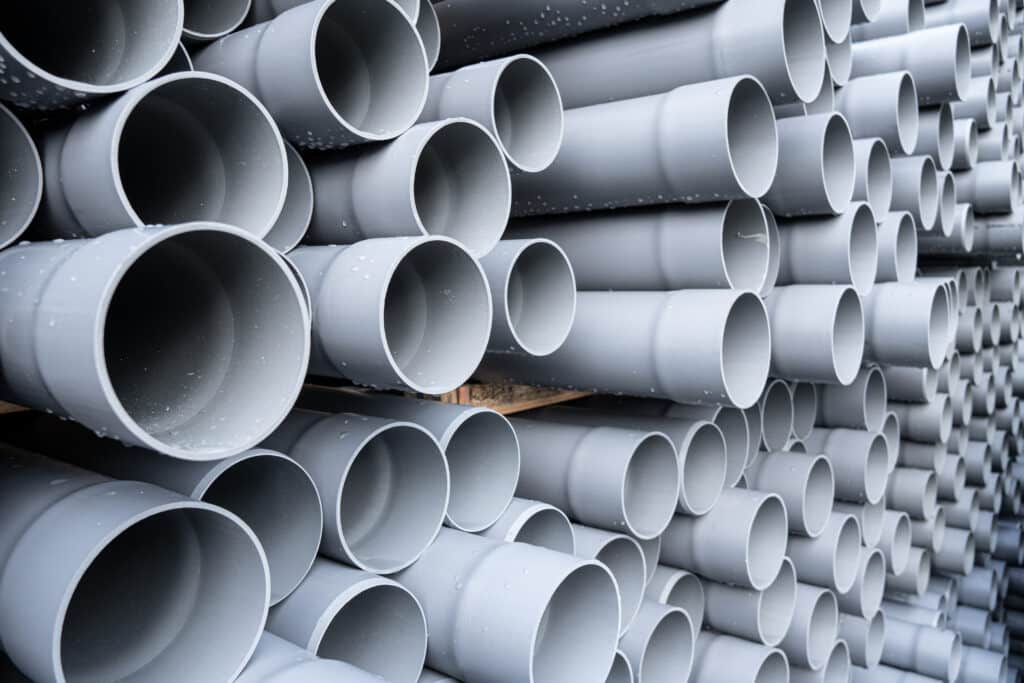
Electrical Nonmetallic Tubing (ENT):
Thin-walled and corrugated, ENT (electrical nonmetallic tubing) is flame retardant but not fire rated. It is not approved for use in exposed locations but is commonly used inside walls or within concrete blocks. Known for its extreme flexibility ENT can be field bent by hand without requiring any special tools or the application of heat. ENT is available in PVC in trade sizes up to 2 inches. Its support spacing is limited to 3 feet and within 3 feet of terminations.
Relevant NEC Codes: Article 362

How to Choose an Electrical Conduit
National Electrical Code (NEC) guidelines, local codes, and engineering specifications most often dictate which conduit to consider for use in a project. Although size and type are key aspects, there are many characteristics to consider when choosing an electrical conduit, including:
- Cable fault
- Toxicity
- Weight
- Durability
- Temperature range
- Support spans
- Burn-through
- Coefficient of friction
- Conductivity
- Distance between expansion joints
- Material cost
- Field handling
- Memory
- Labor cost
The correct conduit should:
- Be durable, corrosion-resistant, and have mechanical strength for project longevity
- Be fire-resistant and non-toxic when burning as dictated by environment/application
- Allow for cables to easily be pulled to areas that may be inaccessible in the future, and unaffected by any pulling lubricants with limited or no burn-through
- Be cost effective with low NECA labor rates
- Be cable fault resistant
- Be lightweight for ease of portability and faster installation
- Support a broad temperature range and UL listed to 110° C
Considerations for Common Electrical Conduit Applications
C&I (Commercial and Industrial) Applications
Steel has traditionally been the conduit of choice for C&I applications, as it provides suitable protection for raceway cables and wire. Unfortunately, steel is also known to be more difficult to field handle (in part due to its heavy weight), and is typically a more expensive option. PVC Coated Rigid Steel conduit & GRC conduit have a much higher installation cost as well.
Engineered for extreme corrosion resistance and UV stability, fiberglass electrical conduit can be substituted for steel in most industrial applications and in a variety of environments, from highly caustic interiors to exposed exterior use cases.
Data Centers
Fiberglass conduit elbows are an ideal choice for protecting data center infrastructure due to their resistance to burn-through, low coefficient of friction, and ability to withstand cable faults.
Traditional materials including galvanized rigid steel, aluminum and PVC-coated steel conduit risk welding wire to the inside of the conduit during fault conditions, while fiberglass conduit remains unaffected.
Fiberglass conduit offers one of the lowest coefficients of friction available for conduit systems and is resistant to any of the current pulling lubricants’ corrosive properties.
Utilities
Fiberglass conduit is well suited for utilities infrastructure with its lightweight, durable construction and is cost-competitive for conduit sizes of 2″ and larger.
The lightweight nature of fiberglass simplifies utility installations, whether above ground or underground, and, per the NECA Manual of Labor Rates, choosing fiberglass conduit can reduce labor costs for your next project.
Unlike PVC pipe which is known to become brittle in low temperatures, fiberglass conduit offers excellent handling in low temperatures. Fiberglass offers a wide temperature range of -60℉ to +250℉ compared to PVC Schedule 40 and Schedule 80’s range of just +40℉ to +150℉ and is UV stable per UL 2515 & CSA C22.2 No. 211.3-96, making it the clear choice for year-round installations.
Bridges, Tunnels and DOT Projects
Galvanized rigid steel conduit (GRC) and PVC-coated rigid metal conduit both have the strength required for bridge and tunnel projects, but often come with a higher price tag. PVC SCH 40, PVC SCH 80 and PVC-coated rigid steel conduit all risk toxicity and release of halogens (i.e. chlorine and bromine) in the event of a fire.
Champion Flame ShieldⓇ Phenolic Conduit is a 2-hour fire rated electrical conduit system that is lightweight and less costly than steel. This phenolic conduit offers best in class field handling due to its light weight, ease of cutting and integral bell, making it the clear choice for subways, tunnels and state DOT (Department of Transportation) projects.
For help selecting a conduit, reach out to an Electrical Sales Rep to learn more.
Additional Resources
This article was originally posted on April 15, 2022, and has since been updated for comprehensiveness.
Recent Blogs
8 Types of Electrical Conduit and Their Uses
What is Electrical Conduit? Electrical conduit is a raceway used to house and protect electrical wires within a building or…
Rep Spotlight: Coleman-Russell & Associates Successfully Targets the Southeastern U.S.
Mechanical agency partner distributes Champion Strut™ with exceptional customer service. Since 1976, Coleman-Russell & Associates has been a premier mechanical…
Meet HR Department Manager: Dina Alvarado
Get to know Dina Alvarado, Champion FiberglassⓇ HR Department Manager. Learn about her background and vision for human resources.