Fiberglass (RTRC) electrical conduit is the best type of conduit to use for underground applications because it is resistant to temperature, moisture and corrosion and is non-toxic, making it an environmentally-friendly option.
Why choosing the correct electrical conduit is important
Electrical conduit provides valuable protection to electrical wiring and electrical cable from moisture, fire, corrosion, impact, electrocution and short-circuits. With many options available to project managers and engineers, it’s important to consider the location and environment specific to each project when selecting an electrical conduit to specify or source. Choosing the wrong conduit can result in risks to safety and significant financial implications.
Underground Electrical Conduit Requirements
UL 2420 BG
This standard details the requirements for low-halogen below ground (Type BG) reinforced thermosetting resin conduit (RTRC) and fittings, for installation and use in accordance with CSA C22.1, Canadian Electrical Code (CE Code), Part I, and NFPA 70, National Electrical Code (NEC).
UL 2420 encompasses ID and IPS conduit and fittings for trade sizes 1/2 (16) to 6 (155), and both encased burial and direct burial conduit.
UL 94 HB
Underground electrical conduit must meet the below ground conduit requirements of UL 94 HB (horizontal burn). Horizontal burn requirements are not as strict as vertical burn requirements, which means that all conduit approved for above ground applications is also suitable for use in below ground (or underground) applications.
NEC Code for Underground Conduit
Article 355 of the National Electrical Code (NEC) details the scope of accepted use, installation, and construction for fiberglass conduit, also known as reinforced thermosetting resin conduit (RTRC), a rigid nonmetallic raceway of circular cross-section, with integral or associated couplings, connectors, and fittings for the installation of electrical conductors and cables. Underground installations are among the approved uses permitted for fiberglass conduit trade size 1/2 through trade size 6.
How Deep to Bury Electrical Conduit Underground?
Depth requirements for buried electrical cable and buried wiring (also known as direct burial installations) can be found in table 300.5 of the NEC (National Electrical Code). Burial depth ranges from 4 inches to 24 inches deep, depending on the type of wiring method used.
Article 300 – General Requirements for Wiring Methods and Materials | ||||||||||
---|---|---|---|---|---|---|---|---|---|---|
Table 300.5 Minimum Cover Requirements, 0 to 1000 Volts, Nominal, Burial in Millimeters (Inches) | ||||||||||
Type of Wiring Method or Circuit | ||||||||||
Location of Wiring Method or Circuit | Column 1 Direct Burial Cables or Conductors | Column 2 Rigid Metal Conduit or Intermediate Metal Conduit | Column 3 Nonmetallic Raceways Listed for Direct Burial Without Concrete Encasement or Other Approved Raceways | Column 4 Residential Branch Circuits Rated 120 Volts or Less with GCFI Protection and Maximum Overcurrent Protection of 20 Amperes | Column 5 Circuits for Control of Irrigation and Landscape Lighting Limited to Not More Than 30 Volts and Installed with Type UF or in Other Identified Cable or Raceway |
|||||
mm | in. | mm | in. | mm | in. | mm | in. | mm | in. | |
All locations not specified below | 600 | 24 | 150 | 6 | 450 | 18 | 300 | 12 | 150 a,b | 6 a,b |
In trench below 50 mm (2 in.) | 450 | 18 | 150 | 6 | 300 | 12 | 150 | 6 | 150 | 6 |
Under a building | 0 | 0 | 0 | 0 | 0 | 0 | 0 | 0 | 0 | 0 |
(in raceway or Type MC or Type MI cable indentified for direct burial) | (in raceway or Type MC or Type MI cable indentified for direct burial) | (in raceway or Type MC or Type MI cable indentified for direct burial) | ||||||||
Under minimum of 102 mm (4 in.) thick concrete exterior slab with no vehicular traffic and the slab extending not less than 152 mm (6 in.) beyond the underground installation | 450 | 18 | 100 | 4 | 100 | 4 | 150 | 6 | 150 | 6 |
(direct burial) | (direct burial) | |||||||||
100 | 4 | 100 | 4 | |||||||
(in raceway) | (in raceway) |
Underground Conduit Options Available
Traditional Metal Conduits
Traditionally, heavy metal conduits made of steel or aluminum were commonly used for a majority of electrical conduit construction projects. In recent years the market has shifted away from traditional metal substrates as lighter, more cost-effective and durable conduits such as RTRC (fiberglass conduit) have become more widely used.
- Rigid Metal Conduit (RMC): RMC is composed of heavyweight galvanized steel, stainless steel, or aluminum, and installed with threaded fittings. RMC is very strong and unfortunately also very heavy, contributing to higher than average cost of both materials and labor.
- Electrical Metallic Tubing (EMT) Thin-walled and unthreaded, EMT is typically made of coated steel or aluminum and used in place of GRC in commercial, industrial, and residential applications. EMT is best for indoor applications and not typically recommended for outdoor or underground electrical applications because of its susceptibility to being damaged easily and need for special watertight fittings.
Fiberglass Conduit
In terms of raw material costs, fiberglass conduit is one of the more affordable electrical conduit options, and it is significantly lighter in weight than traditional conduit materials, resulting in more cost efficient labor installation rates. Fiberglass conduit is an often preferred substrate for utilities, commercial and industrial applications requiring direct burial and encased burial below ground installations because it is resistant to temperature, moisture and corrosion. Also to note, fiberglass conduit is non-toxic, making it an environmentally-friendly option, and chemically inert, which contributes to its longevity. Its light weight and unthreaded joints make it easy (and cost effective) to install, and its low coefficient of friction eliminates the risk of burn-through for long cable pulls.
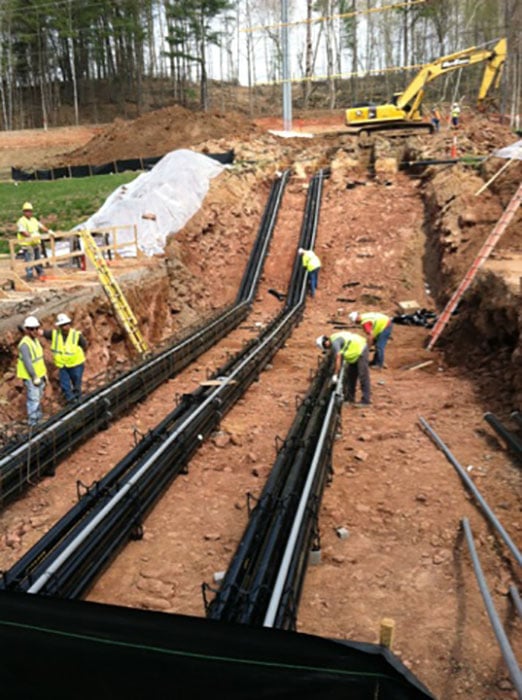
PVC Conduit
Well known for being one of the least expensive electrical conduit, PVC electrical conduit is relatively durable and offers protection from moisture and corrosion. In recent years supply chain issues have significantly increased the cost and lead-times for PVC, leading engineers and contractors to consider substituting more readily available fiberglass conduits. PVC is limited in its temperature range (+40℉ to +150℉), and emits toxic fumes when melted. If your outdoor installation may experience extreme heat or cold, PVC might not be suited for your project.
Which Conduit Is Best for Your Below Ground Application?
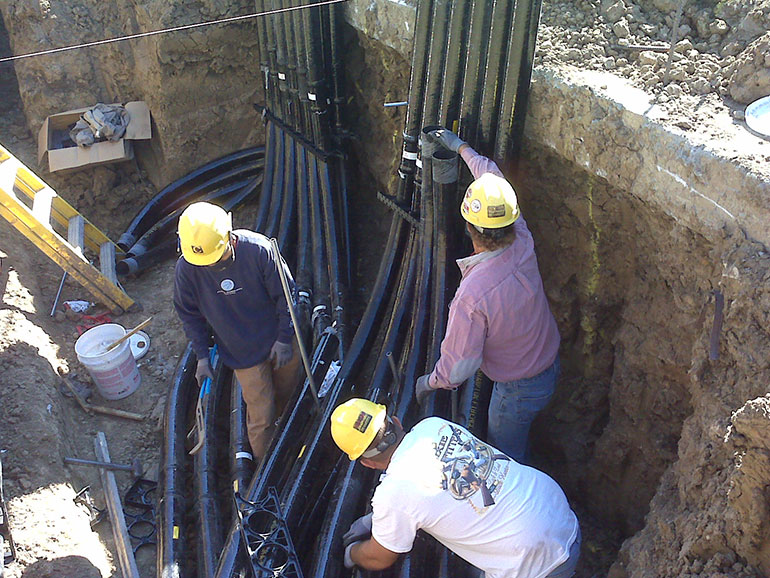
Key factors to consider include:
- The protective qualities of the substrate
- Ease of installation (and the costs associated)
- Long term costs associated with durability and project lifespan
- Up-front materials and labor cost
- Availability and lead times
It’s important to consider a variety of attributes that will affect the lifespan of your installation, not limited to the conduit’s level of corrosion resistance, temperature range and impact resistance.
To compare material and installation costs of fiberglass (RTRC), PVC and a variety of traditional metal conduits including GRC, EMT, aluminum and stainless steel, visit the Champion Fiberglass Conduit Calculator.
For help selecting a conduit, reach out to an Electrical Sales Rep to learn more.
This post was originally published on May 16, 2022 and has been updated for comprehensiveness.
Learn More
Keep Reading
Champion Fiberglass® Named a CompositesWorld Top Shop for 2024
The origins of fiberglass date back to the ancient Greeks. Today fiberglass is used for a variety of applications from…
Get to Know Research and Development Engineer Blake Rogers
He’s got a diverse background in engineering, is new to Texas and can juggle. Meet Blake Rogers.
Electrical Conduit Cost Savings: A Must-Have Guide for Engineers & Contractors
To help identify cost savings that don’t cut corners on quality, Champion Fiberglass developed a free resource for engineers and…