Installation type plays a key role in the type of conduit selected for electrical systems in industrial construction projects. Above ground, below ground, direct buried, encased buried and whether installation is simple or complex — all depend on the project type and environment.
What is the difference between above ground and below ground conduit?
The main difference is fire resistance. Above ground conduit has fire resistance per UL2515 and CSA C22.2 No. 2515 standards, meaning that the conduit will self-extinguish within 15 seconds after each of five successive flame applications per the UL 2515 flame test standard.
Below ground conduit meets UL94 HB (horizontal burn) requirements, which aren’t as stringent as vertical burn requirements. This also means that conduit manufactured and labeled for “above ground” applications can be used for “below ground” applications.
Digging Deeper into Direct Burial Conduit
Direct buried conduit is a type of conduit used in below ground installations of electrical systems in commercial and industrial construction projects. Typically, direct burial conduit is used in applications where there will be minimal digging after installation, as digging has the potential to disrupt and damage conduit (and the cable) buried beneath.
Direct burial serves to protect electrical systems from environmental factors such as trees, branches, wind, and fire plus it can also be an aesthetic solution that hides overhead power lines. Additionally, direct burial conduit is often a solution when electrical systems must cross roadways because it offers less disruption to traffic patterns. Specifically, direct burial is often used in applications such as data centers, waste water treatment facilities and utilities.
Direct buried (DB) conduit must have mechanical strength to withstand the load of the soil thats packed over it. DB quality applications should utilize UL Listed conduit. We typically recommend using our Standard Wall for 3/4″ – 4″ diameter, and Medium Wall for 5″ and 6″ (UL designates Champion Fiberglass MW for 5″ and 6″ as SW). For very deep trenches, special soil conditions or where high rate of compacting can be expected, an even heavier wall should be selected.
Key Considerations for Direct Burial Cable and Conduit in Industrial Construction Projects
When determining whether your below ground conduit installation requires direct burial quality, there are several factors to consider:
- Volatility of the environment. Soil types and load as well as the mechanical strength of the conduit must be considered here. Frost and settlement can impact the stability of direct burial conduit. Corrosion from soil can compromise the conduit as well.
- Compacting of soil. This is an important factor in direct burial conduit. For very deep trenches, special soil conditions or where a high rate of compacting can be expected, a heavier wall conduit should be selected. Contact Champion Fiberglass to answer any questions about the level of compacting in a project.
- Ease of access for later service. Using conduit will allow you to more easily locate and repair cables down the road with less risk of damage to the conduit. Consider a conduit’s coefficient of friction to evaluate for ease of pulling as well as cable fault resistance, which allows a cable to be easily pulled through for repair and replacement.
- Project complexity. Challenging installations can benefit from the efficiency that carefully planned conduit use can provide for cable runs.
- Local regulations. While the NEC (National Electrical Code) may approve a conduit (also referred to as “duct” or “pipe”) use for direct burial, local regulations may call for more stringent installation techniques such as dictating how deep the conduit must be buried.
- Future landscaping. It is important to consider whether future landscaping projects may disrupt direct buried conduit and put the conduit at risk for damage.
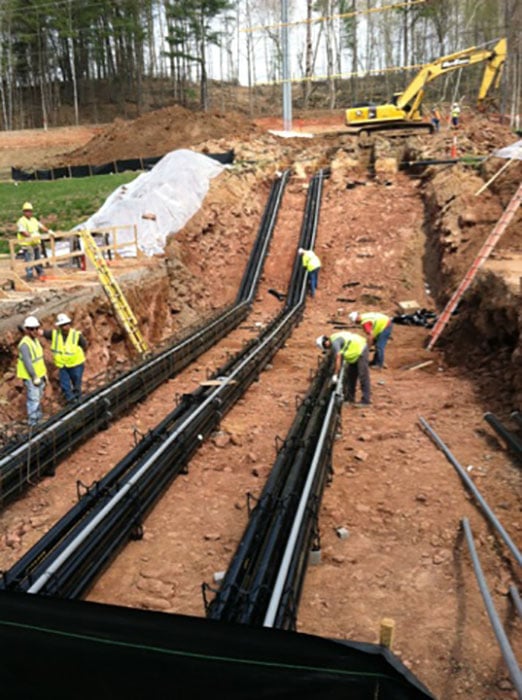
Selecting a Conduit Type
For projects requiring direct burial conduit, selecting the best underground conduit for the job is important. You’ll want to also consider the costs associated with each type of conduit’s raw materials as well as installation, the long-term financial impacts of a conduit’s durability, as well as availability for your substrate of choice. Commonly used conduits for underground applications include traditional metal conduits such as RMC (rigid metal conduit) or EMT (electrical metallic tubing), fiberglass (RTRC) conduit and PVC conduit.
For help selecting electrical conduit, reach out to an Electrical Sales Rep to learn more.
Recent Blogs
8 Types of Electrical Conduit and Their Uses
What is Electrical Conduit? Electrical conduit is a raceway used to house and protect electrical wires within a building or…
Rep Spotlight: Coleman-Russell & Associates Successfully Targets the Southeastern U.S.
Mechanical agency partner distributes Champion Strut™ with exceptional customer service. Since 1976, Coleman-Russell & Associates has been a premier mechanical…
Meet HR Department Manager: Dina Alvarado
Get to know Dina Alvarado, Champion FiberglassⓇ HR Department Manager. Learn about her background and vision for human resources.