The Evolution of Prefabricated Electrical Conduit
“Over the course of a decade, the electrical construction industry has not only made prefab the norm, but also an expectation,” Dr. Perry Daneshgari and Dr. Heather Moore assert in an EC&M article titled, “The Evolution of Prefabrication in the Electrical Construction Industry.” They envision a near future where Prefab Building™ (building with 50%+ prefabricated assemblies) will become more and more prevalent. This shift will require teams to begin projects with prefabrication in mind and challenge them to consider just how much of a project can be completed off-site.
Daneshgari and Moore note that the benefits of prefabrication are significant, “When work is done in a controlled environment, there are fewer obstacles than would be encountered on the job site. Even if the same crew mix is doing the work at the shop, they have less trade interference, less time looking for material, shorter distances to break and a safer environment to work in.”
Despite Daneshgari and Moore’s ambitious predictions for the future, prefabrication is currently largely underutilized in the electrical construction industry. A recent focus group found that 82% of participants were prefabricating less than 10% of their work even though more than half of their electrical work currently being done on-site could be completed off-site.
Extreme Conditions
A key benefit of prefabrication is its ability to mitigate installation challenges caused by extreme weather. For example, during the installation of a solar farm in Arizona temperatures reached a scorching 115℉ and install teams were limited to ten minutes on and ten minutes off working windows. High temperatures like these can cause powered equipment to overheat and also impact torque settings. Conversely, in extreme cold conditions, cable can’t be pulled and cutting precise lengths becomes more challenging.
Prefabrication work done off-site in temperature-controlled environments like warehouses and fabrication shops mitigates and often eliminates these types of weather-related challenges.
Speed and Safety
The Frederick Douglass Memorial Bridge in Washington, D.C. is 1,472 feet long and carries South Capitol Street over the Anacostia River. The project was uniquely challenging in that the project team was only allowed to work on installation one day per week. With high-cost equipment in play, working quickly (while working safely) was paramount to a successful installation.
Champion FiberglassⓇ was selected for all electrical conduit work due to its track record of fast turnarounds, creative custom solutions and the overall safety factors of working with fiberglass (RTRC) over other substrates. The light weight of fiberglass minimized risk by reducing the total time installers would need to handle conduit at dangerous heights.
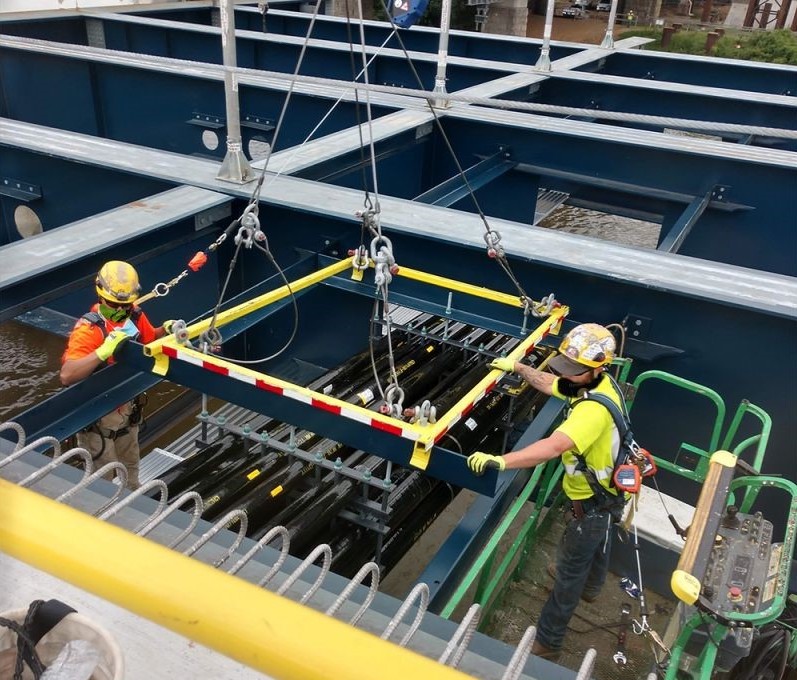
Without utilizing prefabrication the team would not have been able to deliver the electrical conduit with the speed and consistency required to meet the project’s rigid timeline. In addition to prefabrication, the Champion Fiberglass team thoughtfully sourced the right trailers for shipments, allowing more crates to fit per truck and ensuring streamlined storage and installation at the job site. They created customized duct crating and packaging to transport the pre-drilled and pre-assembled ducts and hangers. Once at the job site, the top of the crate could be cut off and the duct package could be picked up directly from the truck for installation. Expansion ducts were built directly into the duct packages to further streamline the process.
Efficiency and Cost Savings
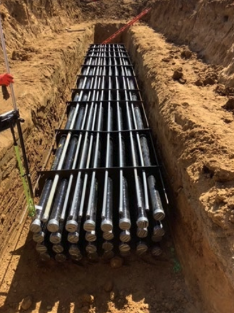
When Rosendin Electric, one of the country’s largest electrical contractors, needed twenty-five miles of 4”, 5” and 6” heavy wall 90s for medium voltage telecom and house transformer duct banks, they elected to use prefabricated fiberglass (RTRC) over PVC. The fiberglass conduit was 66% lighter (at 4”) allowing for a faster, safer and more efficient installation.
Less overall manpower and the ability to use smaller equipment allowed the team to streamline the installation of the prefabricated duct banks. The banks were assembled and dropped directly into the trench via a forklift 20 feet at a time, which would not have been possible with PVC. “To just chip away at that level of footage, 20 feet at a time, is unparalleled. We’d never experienced anything like that,” the Rosendin Electric team commented.
In this case, prefabrication was essential to stay on schedule, and Champion Fiberglass was able to meet 100% of the project’s electrical conduit needs and shave weeks off of the estimated lead times from PVC conduit suppliers.
Identifying and executing opportunities to use prefabricated fiberglass electrical conduit resulted in more than 50% cost savings on materials (vs. PVC) and a total labor savings of 60%.
This level of savings isn’t just limited to switching to fiberglass from PVC, a recent pharmaceutical producer in the Southeast was able to realize 90% material cost savings (at 4”) on fiberglass vs. GRC. Shipping costs for the project were also reduced by preassembling the duct banks before shipping, resulting in a savings of $5,400 per mile.
Challenges Mitigated with Helpful Support
Successful prefabrication projects require detailed planning and exceptional customer support at every stage. The Champion Fiberglass team provided hours of guidance and expertise in partnering with the contractor to develop a customized solution that saved a lot of time and money for the pharmaceutical company. This is just one of many ways the Champion Fiberglass team and its products Do MoreⓇ to help customers reach successful project outcomes.
The result? Fiberglass conduit was successful in saving the pharmaceutical customer thousands of dollars in product, shipping and installation costs while supplying an electrical conduit offering longevity for years to come.
To learn more about how prefabricated fiberglass electrical conduit could save time and money, and improve safety on your next project contact the Champion Fiberglass team directly at 281.655.8900 or info@championfiberglass.com.
Learn More
Keep Reading
Champion Fiberglass® Named a CompositesWorld Top Shop for 2024
The origins of fiberglass date back to the ancient Greeks. Today fiberglass is used for a variety of applications from…
Get to Know Research and Development Engineer Blake Rogers
He’s got a diverse background in engineering, is new to Texas and can juggle. Meet Blake Rogers.
Electrical Conduit Cost Savings: A Must-Have Guide for Engineers & Contractors
To help identify cost savings that don’t cut corners on quality, Champion Fiberglass developed a free resource for engineers and…