• Buried duct banks are used in a variety of industrial construction projects.
• They are typically assembled in a warehouse and are lightweight so they help save installation time.
• Learn about size, installation techniques, materials, heat tolerance, soil compaction, safety regulations, and more.
Why Bury Duct Bank Runs Underground?
Duct bank runs are buried underground primarily to protect the vulnerable electrical wiring within from the often unpredictable elements above. Environmental elements ranging from typical weather cycles to catastrophic natural disasters can wreak havoc on lines supported above grade.
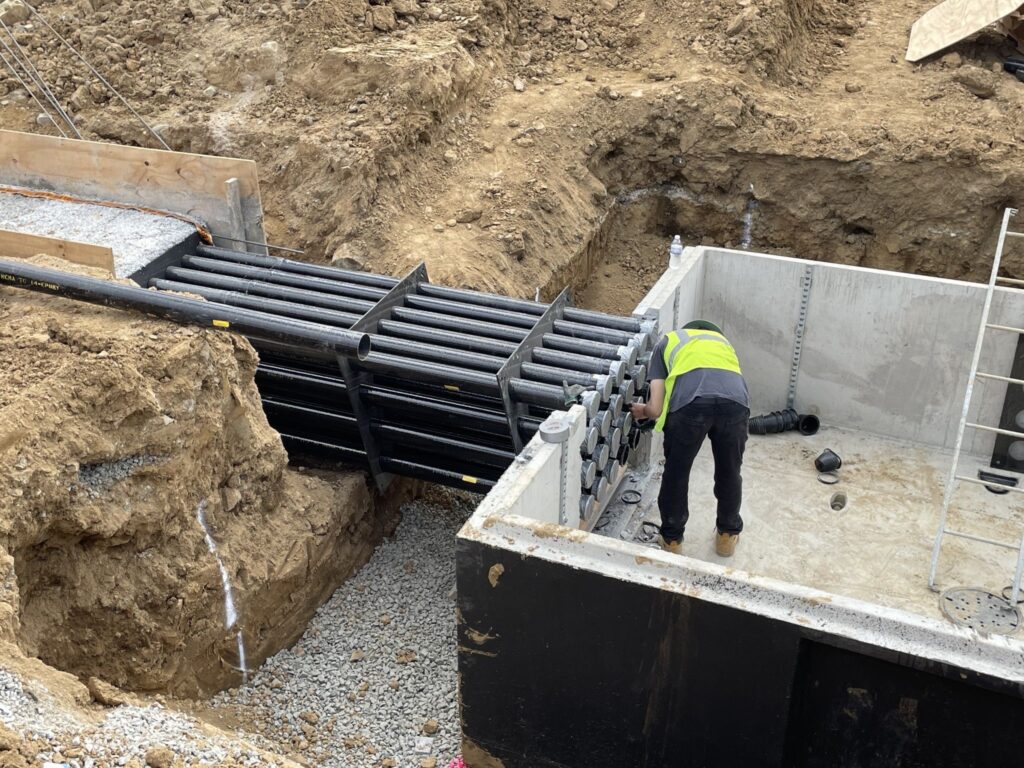
When maintaining the integrity of electrical wiring is mission critical and no above grade disruption can be tolerated underground, electrical duct bank runs are not only more feasible and practical – they’re a necessity.
Although the upfront cost of burying lines can be higher, the long-term benefits often outweigh those costs.
What Types of Locations and Builds Benefit from Underground Duct Banks?
Utilities, data centers, renewables, stadiums, and manufacturing facilities are just a few of the applications that utilize underground duct bank runs. This is because large power draws require secure cable enclosures that are protected from natural and environmental interference.
Considerations for Duct Bank Runs
Stands and Spacers
Stands and spacers, also called frames or chairs, hold the duct in place in a specific pattern. Typically they are made of plastic or HDPE, and may be snap-in style, or only one rung. They may resemble a sheet of plastic with holes cut out of it, or look more like traditional framing. They are a component of nearly every duct bank, serving to keep things organized and allowing the concrete to flow around each duct.
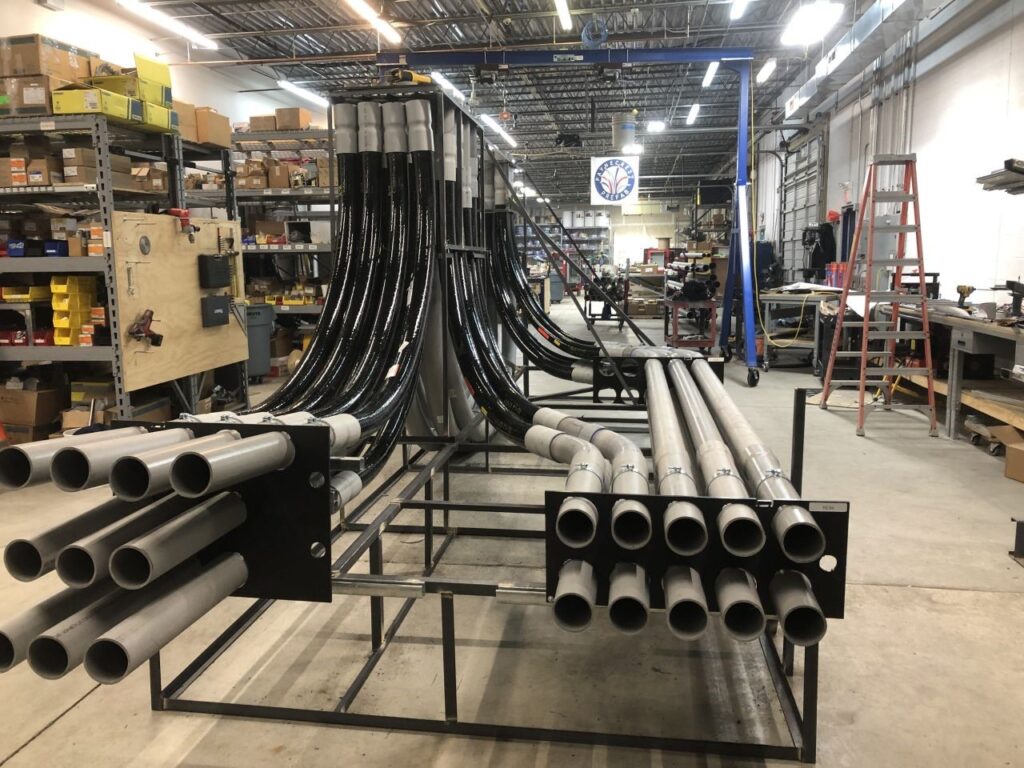
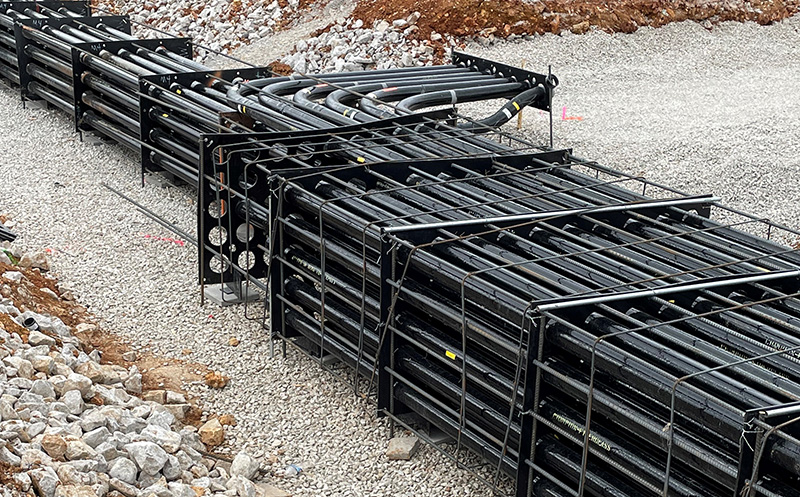
Types of Underground Duct Banks
Encasing electrical duct bank runs with concrete slurry is most common, although some duct banks are direct buried, or filled with gravel. In most cases, concrete will provide the most stable and durable environment.
Open Trench or Trenchless Installation
Traditionally, duct banks have been installed in open trenches where stands are easiest to place and then backfilled with concrete, however trenchless technology continues to grow in popularity.
Trenchless applications are accomplished by using directional boring or drilling using an auger to make a large borehole, then jack and bore to add spacers, before sliding the conduit through and adding high-pressure concrete slurry.
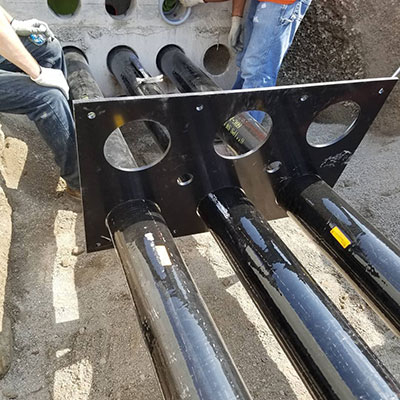
Size
Underground duct bank runs are typically 3×3 or 4×4 with 9 to 16 rungs, but some can go well over 20 and beyond, depending on the scope and scale of the project.
Materials
Corrosion-resistant materials like fiberglass work best with concrete. Surprisingly, concrete is quite corrosive. Fiberglass (RTRC) also dissipates heat well, which is important as duct banks are known to hold a great deal of heat.
PVC is more susceptible to being broken, cracked, or shattered during the backfilling processes compared to other materials.
Aluminum should not be used for underground duct bank applications due to degradation caused by the presence of phosphite.
Metallic conduit will require additional grounding measures to prevent electrical faults or injury due to electrical shock during maintenance or installation.
Installation Techniques
Electrical conduit types have different joining techniques. PVC is typically joined together with glue, while steel is threaded. Fiberglass RTRC is joined with a gasket which allows for quicker installations, as it only needs to be hammered into place to join two pieces.
Step-by-Step Gasket Joint Insertion
Support Spacing
Champion Fiberglass makes an RTRC conduit that is UL-listed for longer support spans than PVC, and comparable spans to GRC duct runs. Greater support spacing allows for fewer spacers or chairs in a duct run, which can lower costs of materials and installation.
Weight
Sometimes duct banks are assembled before they are dropped into the trench. Fiberglass RTRC is one-third of the weight of PVC and one-tenth of the weight of steel. Why does weight matter? Not only is lifting a bank of twelve 20-foot sections plus spacers made out of lightweight fiberglass much easier than lifting the same sections made out of PVC or GRC (galvanized rigid steel), it’s safer, faster and often more economical.
Coefficient of Friction
Selecting a material with a low coefficient of friction can reduce the number of vaults used in a duct bank run and save on project costs. Vaults are pull points to pull cable from one run of duct bank to the next. The heavy weight of the cables limits the amount of force that can be exerted to pull them safely. A material with a low coefficient of friction allows for longer pulls and a reduction of cost from $10K to $100K per pull point or vault.
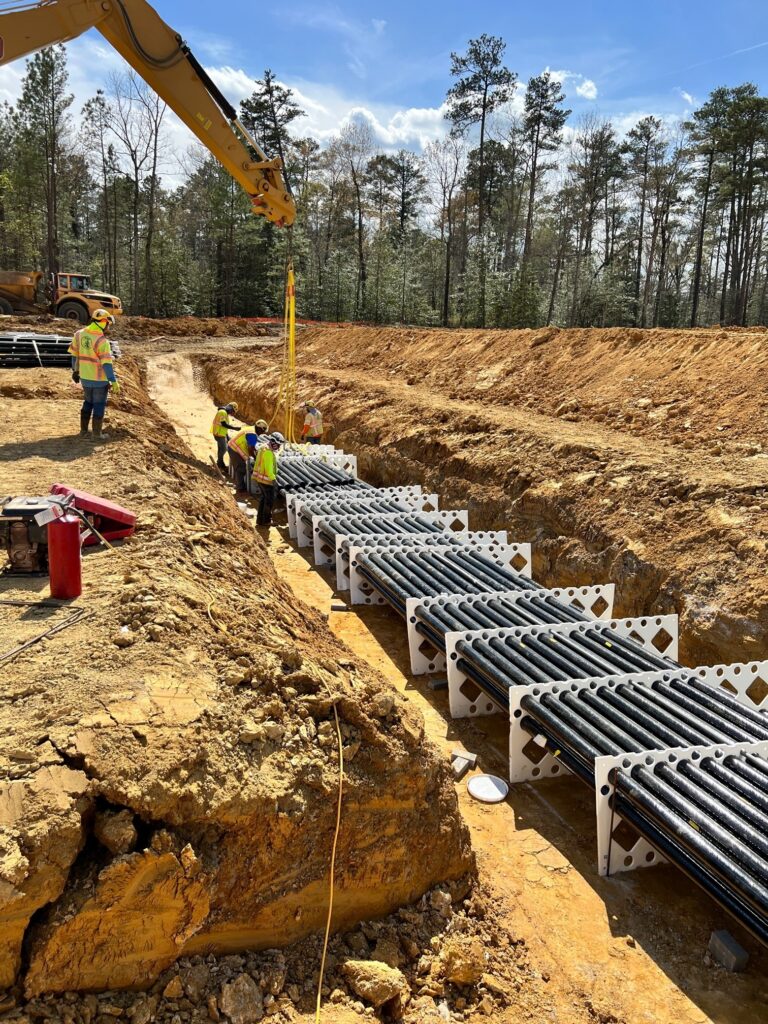
Heat Tolerance
Dense cables can generate heat within conduits. PVC conduit is UL Listed to 90ºC while fiberglass (RTRC) conduit is UL Listed to 110ºC. The higher heat rating is preferred as it allows more flexibility for design engineers.
Soil Compaction
Appropriate soil compaction will ensure stability and protect the duct bank from future damage. Engineering specifications as well as local building codes will determine the appropriate social compaction requirements for each project.
Safety Codes and Regulations
The National Electrical Code (NEC), National Electrical Safety Code (NESC), and local building codes each include safety requirements regarding depth, grounding and spacing of duct banks. During installation teams must also follow all applicable OSHA regulations.
Emergency Repairs, Testing, and Inspections
Predefined procedures for locating, isolating, removing and replacing damaged sections, as well as plans for coordination with utility companies and contractors, are critical for the longevity and reliability of a duct bank system. Prior to entering service, and on an ongoing basis, the duct bank will require inspections that may include insulation resistance testing (megger test), high-potential (hi-pot) testing, electrical system design, and safety systems testing.
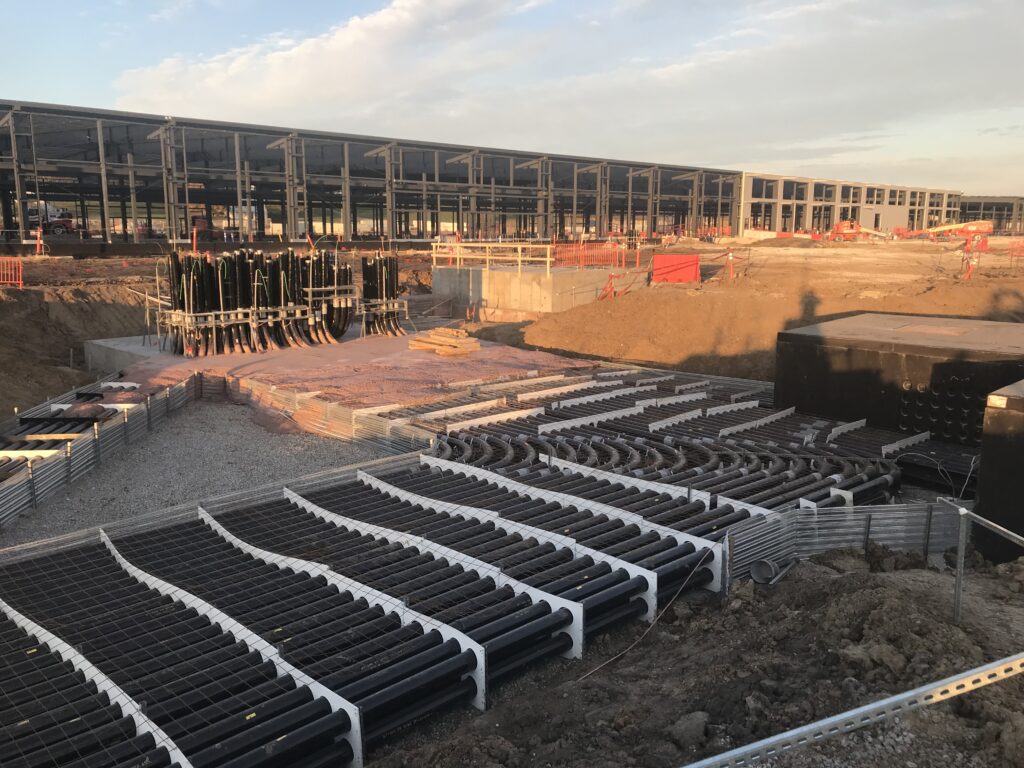
See it in Action
Learn how prefabricated duct banks can result in 50% cost savings (vs. PVC):
FAQs
What is a duct bank in electrical systems?
A duct bank is a structure designed to organize, protect and house electrical cables and conduit.
How deep should a duct bank be installed?
The minimum depth for most duct banks is 24 inches
What are the most common duct bank installation issues?
Improper depth or spacing, drainage issues, cable damage during pulling and failure to meet local requirements are common duct bank installation issues.
Want to Learn More About Considerations for Duct Bank Runs?
Reach out to your local Rep or contact us directly to learn more.
This article was originally posted on November 16, 2023, and has since been updated for comprehensiveness.
Learn More
Recent Blogs
8 Types of Electrical Conduit and Their Uses
What is Electrical Conduit? Electrical conduit is a raceway used to house and protect electrical wires within a building or…
Rep Spotlight: Coleman-Russell & Associates Successfully Targets the Southeastern U.S.
Mechanical agency partner distributes Champion Strut™ with exceptional customer service. Since 1976, Coleman-Russell & Associates has been a premier mechanical…
Meet HR Department Manager: Dina Alvarado
Get to know Dina Alvarado, Champion FiberglassⓇ HR Department Manager. Learn about her background and vision for human resources.