- Supply chain issues continue to plague the construction industry
- The PVC shortage has potential to continue through 2024
- Fiberglass conduit is a superior replacement for PVC SCH 40 that is available with shorter lead times and lower prices
- Projects utilizing fiberglass conduit benefit from its light weight, durability and less costly installation
For PVC pipe it might be a new year, but buyers are seeing the same shortages and skyrocketing prices. COVID-19 precautions, labor shortages, the availability of important chemicals, and global supply chain disruptions continue to contribute to rising costs and limited availability of many products, including PVC conduit.
Where We’ve Been, And Where We’re Headed
In 2020, five hurricanes (Cristobal, Marco, Laura, Delta, and Zeta) caused major disruptions for many Gulf Coast producers, including LyondellBasell and Chevron Phillips Chemical. At the time, experts predicted it would take 6 months for production in Texas to return to normal.
Unfortunately, the Gulf Coast freeze Texas experienced in February 2021 further devastated the plastics industry. The winter storm shut down the world’s largest petrochemical complex and for nearly a month polyvinyl chloride (PVC) production was offline, causing PVC export prices to double to record highs.
Then came the Suez Canal cargo ship blockage, which further impacted the plastics supply chain in March of 2021. Throughout the year rapidly rising shipping prices for goods from Asia reduced the already limited inventory entering the United States, as demand for plastic resins in the consumer packaging sector continued to rise to support major shifts towards online shopping during the pandemic.
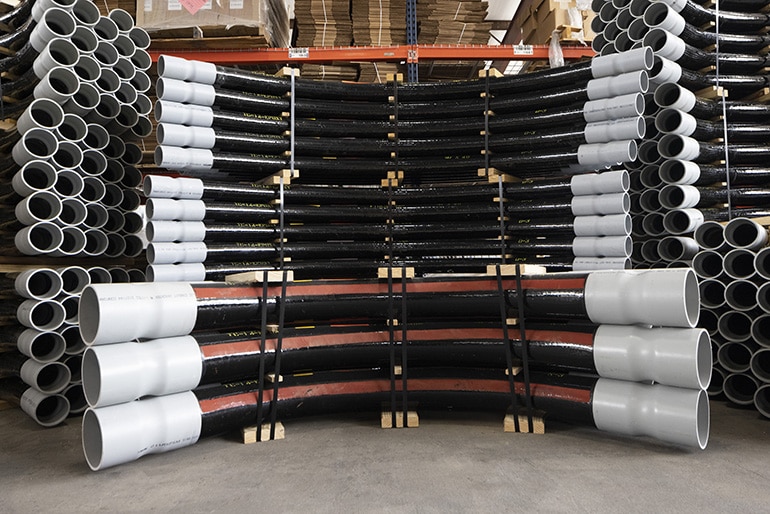
That e-commerce growth has also fueled warehouse construction. Construction starts increased in 2021 and are expected to continue to increase in 2022, with commercial construction projected to grow by 10% this year. Data center builds as well as highway and bridge construction are all expected to continue to increase in 2022, further driving demand for reliable electrical conduit that can be delivered on time and within budget.
What Market Leaders Are Saying
As we enter 2022, PVC producers continue to struggle to restock inventories and fill backorders, and unprecedented supply chain issues and labor shortages further complicate their ability to deliver product.
The ICIS (Independent Commodity Intelligence Services) reports that the cost of PVC was up 70% in 2021 across a variety of PVC goods from pipe to credit cards. More recently, Border States Supply Chain Solutions reported in December of 2021 that “the cost of PVC pipe has been highly impacted over the past two years, up 400%-500% due to these resin constraints.”
Are record high prices here to stay? In 2022, yes. A&B Plastics and Fabrications owner Mark Gilliam said in October of 2021, “I wouldn’t expect a big change in the next year.” Survey data from AlixPartners expect that shortages related to resin could continue through 2024.
Liz Lipply, manager of customer service and marketing at Ferriot, says “this affects anybody that makes plastic parts – everything from consumer goods to industrial products,” and the injection molding company recommends that its customers approve multiple resins for use in their projects to better mitigate issues during shortages.
Rising product costs should also push engineers and project managers to consider where else costs might be mitigated beyond raw materials. When specifying electrical conduit, light weight yet strong substrates like fiberglass (RTRC) are considerably less costly to install, and have not been affected by the shortages plaguing the PVC markets.
PVC Alternatives for Electrical Conduit Projects
Lead time and lasting price increases are expected to continue to affect PVC project budgets throughout 2022. Many project managers are switching to alternative conduits including fiberglass (RTRC) conduit. USA-made fiberglass conduit from Champion Fiberglass is an ideal substitute.
Compared to PVC, Champion Fiberglass conduit is cost-competitive on sizes 2” and above and installation labor hours are considerably less than that of competitive substrates per the NECA Manual of Labor Rates, due to fiberglass’s low weight. For example, one hundred feet of 4” SW RTRC conduit weighs 72 pounds while the same 100 feet of SCH 40 PVC weighs 231 pounds, a weight difference of 3 times.
Fewer pull boxes are required for fiberglass conduit installations due to lower cable coefficient of friction allowing for longer cable pulls. Greater impact resistance and superior durability contribute to additional cost savings of fiberglass conduit vs. PVC over the lifetime of the install.
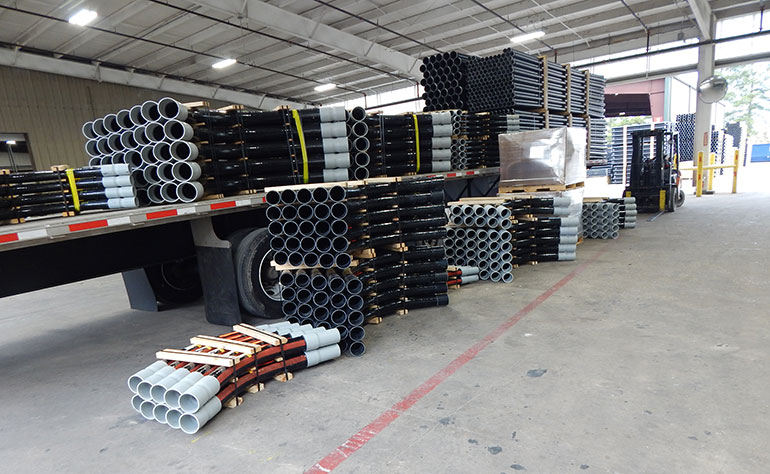
Broader temperature ranges for RTRC (-60°F to +250°F versus +40°F to +150°F for PVC SCH 40 and PVC SCH 80) ensure that for most project environments, fiberglass is a suitable, if not superior, alternative.
Also contributing to safer conditions for the life of the installation, fiberglass does not release toxic halogens (i.e. chlorine and bromine) when burning, unlike conduit systems PVC SCH 40, PVC SCH 80, and PVC coated steel conduit.
For a full comparison of fiberglass conduit to PVC SCH 40, PVC SCH 80, and PVC-coated steel, download the Conduit Comparison Chart to learn how engineers and project managers can Do More® with fiberglass conduit.
Recent Blogs
8 Types of Electrical Conduit and Their Uses
What is Electrical Conduit? Electrical conduit is a raceway used to house and protect electrical wires within a building or…
Rep Spotlight: Coleman-Russell & Associates Successfully Targets the Southeastern U.S.
Mechanical agency partner distributes Champion Strut™ with exceptional customer service. Since 1976, Coleman-Russell & Associates has been a premier mechanical…
Meet HR Department Manager: Dina Alvarado
Get to know Dina Alvarado, Champion FiberglassⓇ HR Department Manager. Learn about her background and vision for human resources.