In industrial and commercial settings, proper electrical conduit burial depth is crucial for enhancing safety, compliance, and long-term operational efficiency. Burial depth can significantly impact system performance, maintenance requirements, and overall project costs.
Burial Depth Considerations for Industrial and Commercial Applications
- High Voltage Considerations: Industrial and commercial installations often incorporate high-voltage systems, requiring deeper burial to ensure adequate insulation and safety. The National Electrical Code (NEC) stipulates minimum burial depths based on voltage ratings, with higher voltages generally requiring greater depths.
- Heavy Traffic Areas and Load-Bearing Surfaces: In industrial complexes and commercial zones, conduits may need to be buried beneath areas subject to heavy vehicular traffic or substantial loads. Deeper burial helps protect conduits from physical stress and potential damage.
- Chemical Exposure and Corrosive Environments: Many industrial settings involve exposure to harsh chemicals or corrosive substances. Burial depth can play a role in mitigating these risks, especially when combined with appropriate conduit materials like RTRC fiberglass.
- Electromagnetic Interference (EMI): Certain industrial equipment can generate significant electromagnetic fields. Proper burial depth, along with the right conduit material, can help shield sensitive circuits from EMI.
- Type of Conduit Material: Different substrates have different requirements. For example, PVC conduit is more vulnerable to damage and generally requires deeper burial compared to metal conduit.
- Soil Conditions: The type and stability of soil can affect the required depth. Rocky or unstable soil may necessitate deeper burial.
- Climate and Environmental Factors: Regions with extreme weather conditions, such as freezing temperatures, may have specific depth requirements to prevent damage from frost heave.
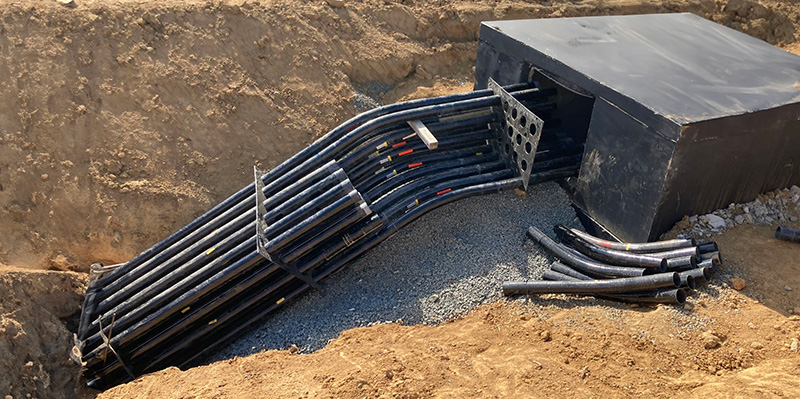
National Electrical Code (NEC) Conduit Requirements
The 2023 National Electrical Code (NEC) provides specific guidelines for conduit burial depths in Table 300.5. For instance, rigid metal conduits carrying circuits rated 1,000 volts or less must be buried at least 6 inches deep, unless they are buried under airport runways where they must be buried at least 18 inches deep, or under highways, roads or parking lots where they require a minimum of 24 inches of burial depth. However, these are just baseline requirements, and local codes or specific environmental factors may necessitate deeper burial.
Local Building Codes
In addition to the NEC, local building codes may have specific requirements for conduit burial depths. Always check with local authorities to ensure all application regulations are followed.
How Deep to Bury Electrical Conduit in Standard Applications
Commercial Installations
In commercial settings, the required depth can vary based on the type of conduit and expected load. Generally, a minimum depth of 24 inches is recommended for nonmetallic conduit, while metal conduit may require 6 to 12 inches.
Industrial Installations
Industrial installations often require deeper burial due to higher load and traffic considerations. A minimum depth of 24 to 36 inches is common for both nonmetallic and metal conduits in these environments.
Best Practices for Industrial and Commercial Conduit Burial
- Trenching: Use appropriate machinery for large-scale trenching, ensuring consistent depth and proper bedding.
- Bedding and Backfill: Use clean, compactable material for bedding and initial backfill to provide uniform support and protection.
- Warning Systems: Install warning tape or other indicators above the conduit to alert future excavators.
- Quality Control: Implement rigorous inspection and documentation processes throughout the installation.
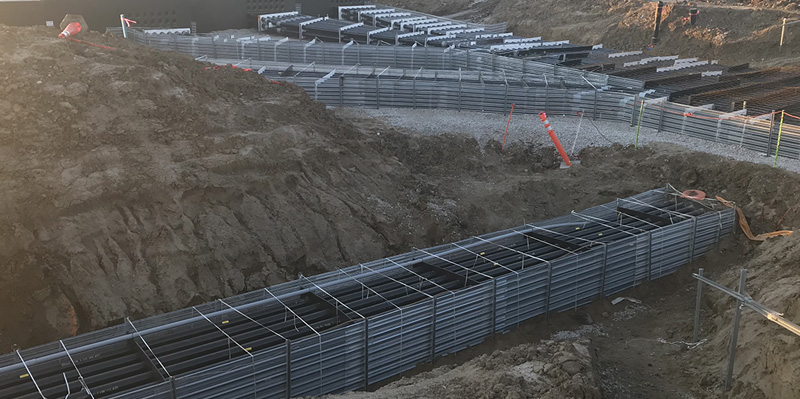
Common Installation Mistakes and How to Avoid Them
Incomplete Excavation
After digging the trench to the required depth, ensure that the bottom is smooth and free of sharp objects.
Incorrect Depth
Failing to bury the conduit to the correct depth can lead to damage and non-compliance. Always double-check depth requirements and measurements, and check the trench depth periodically during installation to make any necessary adjustments.
Poor Soil Compaction
Improper compaction of the soil around the conduit can cause it to shift or become damaged. Ensure thorough compaction during backfilling.
Neglecting Local Codes
Ignoring local building codes can result in fines and required rework. Always verify local requirements before beginning installation.
Troubleshooting and Maintenance
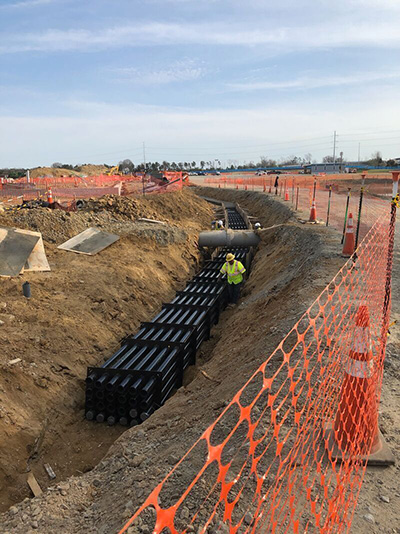
Signs of Improper Installation
Look for signs such as exposed conduit, uneven ground above the conduit, or electrical issues that may indicate improper installation.
How to Address Issues
If installation issues, such as incorrect depth or damaged conduit are discovered, take immediate action to correct them, including re-excavating and re-laying the conduit if necessary.
Routine Inspections
Conduct regular inspections of the conduit to ensure it remains in good condition and complies with all regulations.
Fiberglass Conduit: The Superior Choice
Fiberglass (RTRC) conduit offers several advantages that make it an excellent choice for industrial and commercial applications, often allowing for shallower burial depths without compromising safety or performance:
- Corrosion Resistance and Longevity: Unlike metal conduits, fiberglass is inherently resistant to corrosion, even in harsh chemical environments. This resistance allows for potentially shallower burial in corrosive soils without risking premature degradation.
- Weight Advantages: Fiberglass conduit is significantly lighter than metal conduits, making installation easier and potentially reducing the need for heavy machinery during burial, especially in deeper installations.
- Thermal Stability: With a low coefficient of thermal expansion, fiberglass conduit maintains its integrity across a wide temperature range, reducing the risk of damage due to thermal stress and potentially allowing for more flexible burial depth options.
- Non-Conductive Properties: Fiberglass conduit is non-conductive, allowing for safer installations and maintenance, while ensuring excellent insulation properties.
Burial Depth Comparisons
- Fiberglass vs. RMC: While both may have similar NEC-mandated minimum depths, fiberglass conduit corrosion resistance and lighter weight can make shallower installations more feasible in certain environments.
- Fiberglass vs. PVC: Fiberglass generally offers superior strength and chemical resistance, potentially allowing for shallower burial in areas where PVC might require deeper installation for protection.
Fiberglass Conduit in Challenging Environments
Fiberglass has proven particularly effective in demanding industrial settings:
- Chemical Plants and Refineries: Chemical resistance makes fiberglass conduit ideal for these corrosive environments.
- Data Centers: Fiberglass conduit’s non-conductive nature helps maintain signal integrity in dense cable installations.
- Transportation Infrastructure: Its durability and resistance to vibration make fiberglass a superior choice for airports and railways.
Determining the appropriate burial depth for electrical conduit in industrial and commercial settings requires careful consideration of various factors, from voltage ratings to environmental conditions. While adhering to NEC and local code requirements is essential, the choice of conduit material can significantly impact installation practices and long-term performance. Fiberglass conduit, with its unique properties, often emerges as a superior choice, potentially allowing for more flexible burial options while enhancing safety, longevity, and optimal performance in challenging industrial and commercial environments.
For more information on how fiberglass conduit can benefit industrial or commercial projects, contact the Champion Fiberglass team directly at 281.655.8900 or info@championfiberglass.com.
Learn More
Recent Blogs
8 Types of Electrical Conduit and Their Uses
What is Electrical Conduit? Electrical conduit is a raceway used to house and protect electrical wires within a building or…
Rep Spotlight: Coleman-Russell & Associates Successfully Targets the Southeastern U.S.
Mechanical agency partner distributes Champion Strut™ with exceptional customer service. Since 1976, Coleman-Russell & Associates has been a premier mechanical…
Meet HR Department Manager: Dina Alvarado
Get to know Dina Alvarado, Champion FiberglassⓇ HR Department Manager. Learn about her background and vision for human resources.