By Scott Patchan
In utility projects, underground conduit systems must be resilient, cost-effective, and support efficient cable pulling through various terrain. However, traditional materials often introduce challenges, including elbow burn-through, complex installations, heavy conduits, long pulls, and high costs. Let’s break down each of these issues and explore how fiberglass conduit elbows provide a solution.
Utility Project Challenges
1. Cost: Traditional conduit materials like steel and PVC-coated steel are significantly heavier than others. Heavier conduit increases labor, material costs, and handling challenges.
2. Complex Buried Installation: Utility projects frequently involve complex, underground installation. Heavy conduit materials require not only extensive equipment but also manpower, adding risk and time to the installation.
3. Elbow Burn-Through: Traditional elbows used in underground systems, such as PVC, can experience burn-through, particularly with high friction from dense, extended cable pulls. Burn-through compromises system integrity and requires costly conduit repairs or replacements.
4. Long Cable Pulls: Long pulls with traditional conduit can produce excessive friction, increasing installation time and the likelihood of conduit or cable damage, particularly at bends.
5. Fault concerns: Cable faults that meld or weld to the inside of the conduit cause expensive repairs.
Fiberglass Conduit Elbows: Practical Solutions for Utilities
Fiberglass conduit elbows address each of these challenges, providing essential benefits that lead to better project outcomes.
Lower Material and Installation Costs: Fiberglass elbows are significantly lighter than alternatives GRC, PVC-coated steel and most sizes of PVC, lowering material and installation costs. Labor is reduced because the lightweight material allows installers to position and connect elbows faster without specialized equipment. Made in America fiberglass conduit offers substantial savings in both material costs, labor efficiency, and also shipping costs.
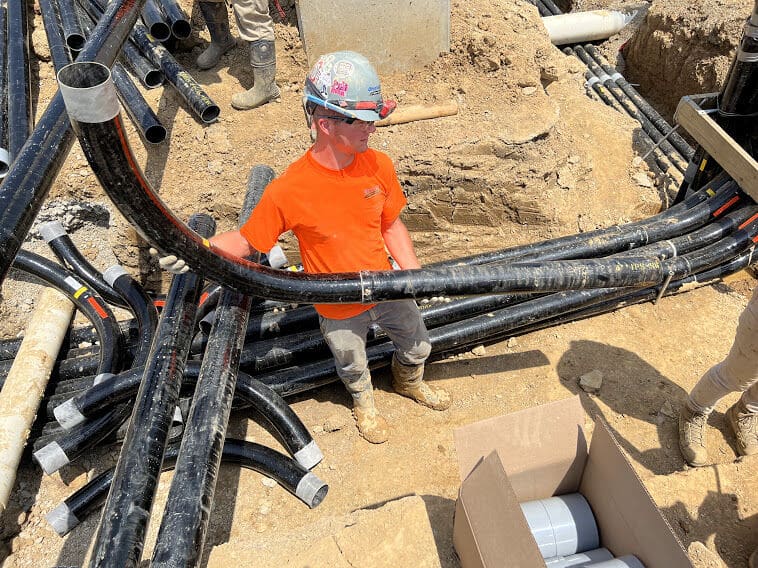
Seamless Installation: Fiberglass elbows are lighter and easier to handle than traditional options, simplifying buried installations. Fiberglass installs faster than many sizes of electrical conduit types per the NECA Manual of Labor Units. Contractors are frequently amazed at the ease with which a single elbow can be picked up by a person at the jobsite. Additionally, gasketed connections speed installation and reduce the need for heavy equipment, lowering costs and installation risks in tight or challenging spaces.
No Burn-Through: Fiberglass conduit’s mechanical strength withstands high-tension cable pulling without burn-through. And flexural strength helps eliminate the risk of cable damage when pulling. This reliability eliminates the risk of elbow damage in high-stress areas, lowering maintenance needs.
Low Coefficient of Friction: With a low coefficient of friction, .38 compared to .55 for PVC-coated steel and galvanized rigid steel and .90 for SCH 40 and 80, fiberglass allows cables to be pulled more smoothly through conduit with less labor time, cost and risk.
Cable Fault Resistance: Fiberglass conduit is cable fault resistant meaning the wire does not melt to the inside of the conduit. This means damaged or faulted cable can be easily pulled through and replaced, since the conduit has not been damaged.
Case Study Summary: Fiberglass Conduit Success in a Data Center
In Virginia’s Data Center Alley, contractor Rosendin Electric faced an extensive installation for telecom and transformer duct banks. Opting for Champion Fiberglass® conduit and elbows, the project benefited from fiberglass’s lightweight structure, reducing equipment needs and enhancing safety in the trench. Prefabricated duct banks further streamlined installation, with Champion Fiberglass providing essential guidance and support throughout the process. Compared to PVC, fiberglass lowered material costs by almost 50%, while total labor savings reached 60%. The project achieved a 63% productivity increase over traditional materials, allowing it to finish on time and on budget.
Get the full details of this case study here.
Fiberglass conduit elbows offer transformative benefits for utility projects, addressing common challenges with solutions that prioritize durability, ease of installation, and cost efficiency. For projects requiring resilient underground infrastructure, fiberglass presents a smart, reliable choice.
Learn More
Recent Blogs
8 Types of Electrical Conduit and Their Uses
What is Electrical Conduit? Electrical conduit is a raceway used to house and protect electrical wires within a building or…
Rep Spotlight: Coleman-Russell & Associates Successfully Targets the Southeastern U.S.
Mechanical agency partner distributes Champion Strut™ with exceptional customer service. Since 1976, Coleman-Russell & Associates has been a premier mechanical…
Meet HR Department Manager: Dina Alvarado
Get to know Dina Alvarado, Champion FiberglassⓇ HR Department Manager. Learn about her background and vision for human resources.